Wie unser Heckdifferential-Träger für den VW T4 Syncro entstand – Ein Blick hinter die Kulissen
Wer einen VW T4 Syncro fährt, weiß: Ersatzteile für bestimmte Baugruppen werden zunehmend rar. Gerade beim vorderen Querträger des Heckdifferentials ist das Angebot entweder vergriffen, rostgeplagt oder qualitativ fragwürdig. Deshalb haben wir es uns zur Aufgabe gemacht, dieses Bauteil nicht nur nachzubauen – sondern besser zu machen. In diesem Blogbeitrag zeigen wir dir Schritt für Schritt, wie unser neuer Querträger für den T4 Syncro entstanden ist.
1. Vermessung per 3D-Scan: Der erste Schritt zum digitalen Zwilling
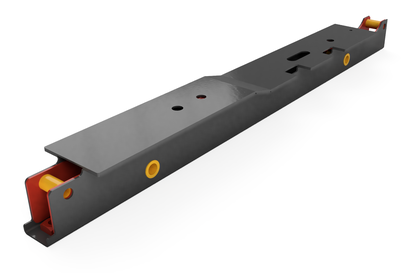
Alles begann mit einem Originalteil aus einem Syncro-Kastenwagen. Um möglichst exakte Daten zu erhalten, wurde der Träger inklusive Halterungen mit einem hochauflösenden 3D-Scanner erfasst. Das Ziel war klar: Wir wollten ein digitales Modell schaffen, das jedes Detail des Originals exakt abbildet – als Basis für alle weiteren Arbeitsschritte.
2. Manuelle Nachvermessung: Technik ist gut – Kontrolle ist besser
So präzise ein 3D-Scan auch ist – wir wollten auf Nummer sicher gehen. Deshalb haben wir sämtliche wichtigen Maße zusätzlich manuell überprüft. Kritische Stellen wie Schraubpunkte, Radien, Biegekanten und Auflageflächen wurden nochmals von Hand abgenommen. So konnten wir Ungenauigkeiten ausgleichen und sicherstellen, dass später alles perfekt passt.
3. CAD-Rekonstruktion in Fusion 360: Das virtuelle Modell entsteht
Mit den kombinierten Messdaten ging es in die CAD-Software. In Fusion 360 wurde jedes einzelne Bauteil von Grund auf neu konstruiert. Dabei haben wir uns eng an der Originalgeometrie orientiert – mit einem entscheidenden Unterschied: Bereits in diesem Schritt flossen erste Verbesserungen in das Design ein.
4. Optimierung für Stabilität & Lebensdauer
Unser Ziel war nicht nur ein Ersatz – wir wollten ein Upgrade. Deshalb haben wir folgende Änderungen umgesetzt:
- Materialwahl: Statt dem üblichen 1,5 mm Blech verwenden wir robustes 2 mm Stahlblech.
- Verstärkte Mutternaufnahmen: Die Aufnahmen für die Differentialhalter bestehen aus Muttern mit höherer Festigkeit als im Originalteil.
- Zusätzliche Verschraubungspunkte: Für die Montage eines möglichen Unterfahrschutzes haben wir zusätzliche Befestigungsgewinde vorgesehen.
- Passgenauigkeit: Biegungen, Winkel und Geometrien wurden so überarbeitet, dass der Einbau möglichst stressfrei gelingt – ohne Nacharbeiten.
5. Kontrolle & Abgleich: CAD vs. Realität
Bevor es in die Fertigung ging, haben wir unser CAD-Modell nochmals akribisch mit dem Original abgeglichen. Alle Maße wurden nochmals überprüft, um sicherzustellen, dass das digitale Modell mit der Realität übereinstimmt. Denn bei einem Bauteil, das Teil eines Allradantriebs ist, darf es keine Kompromisse geben.
6. Planung der Fertigung: Vom digitalen Modell zum greifbaren Teil
Nachdem die Konstruktion abgeschlossen und freigegeben war, haben wir die Fertigung vorbereitet. Die Wahl fiel auf lasergeschnittene und CNC-gekantete Bleche aus hochwertigem Stahl. Alle Komponenten wurden exakt nach den CAD-Daten produziert – millimetergenau und serienfähig.
7. Beschichtung & Hohlraumversiegelung: Schutz auf allen Ebenen
Um dem Rost dauerhaft die Stirn zu bieten, setzen wir auf eine galvanische Verzinkung aller Komponenten. Doch damit nicht genug: Der Träger wird innen hohlraumversiegelt, bevor er unser Lager verlässt. So stellen wir sicher, dass er nicht nur optisch hochwertig wirkt, sondern auch im harten Alltag zuverlässig hält.
Fazit: Besser als das Original

Mit diesem Projekt haben wir nicht einfach ein Ersatzteil nachgebaut – wir haben eine Lösung entwickelt, die durchdacht, verbessert und praxistauglich ist. Wer seinen VW T4 Syncro langfristig erhalten will, bekommt bei uns ein hochwertiges Bauteil, das mit Leidenschaft, Präzision und einem tiefen Verständnis für den T4 entwickelt wurde.
Produktionsstart ist KW 18-2025